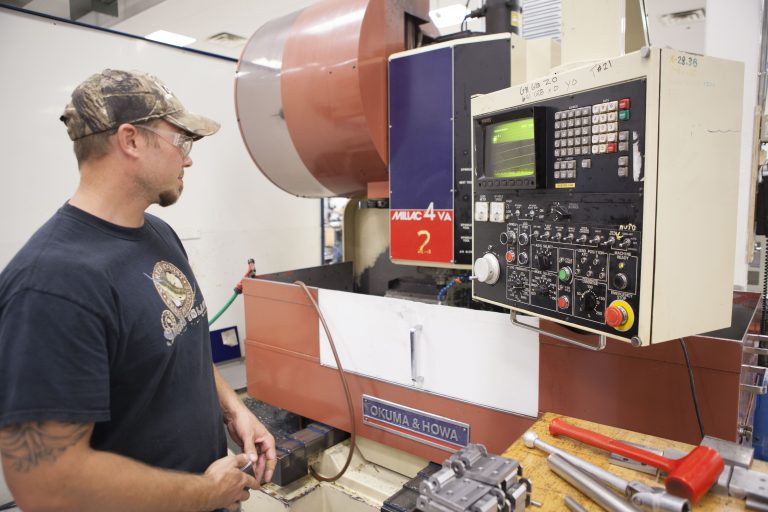
Nearly 50 percent of American employers report having difficulty filling open positions in Manpower Group’s 2018 Talent Shortage Survey. Of those open positions, skilled trades – such as electricians, welders and mechanics – are the hardest to fill. As the talent gap continues to be an issue at a national, statewide and local level, Afterschool Download is providing a four-part series focused on all things skilled trades. In part two, we look at opportunities for advancement within manufacturing
Pipe coupling manufacturer Fernco has multiple job openings for machine operators. It’s an entry-level position – and a stepping stone for career growth.
“We have an internal job posting program,” says Vicki West, director of Enterprise Development at the Davison-based company. “We’ve had a lot of employees advance within the plant, and many with and without college degrees have transferred from the shop to our customer service, IT and human resource departments.”
Even Fernco President Mark Cooper got his start running the machines, West adds. “You learn the business from the ground up when you start on the factory floor.”
Despite the opportunity for career advancement, manufacturing jobs face a perception problem. In a 2014 report from Deloitte and the Manufacturing Institute, Americans rank manufacturing fifth in career choice for themselves when provided with seven possible industry options. Additionally, only 37 percent of respondents say they would encourage their children to pursue a manufacturing career.
At the same time, survey respondents cited interesting work and the ability to build skills on the job among the most important criteria when selecting a job. And according to Grand Blanc-native Derek Ream, working at Fenton-based Miller Industries has afforded him just those opportunities.
“I had been working as a travel agent and just wanted to try something different,” says Ream, who took an entry level job processing sheet metal at Miller Industries in early 2017. “Six months in, I went out on a couple of service jobs with the head electrician and really enjoyed myself.”
When Miller Industries launched its new apprenticeship program for electricians earlier this summer, company management asked Ream if he’d like to be involved. The 22-year-old has been training on the job ever since and will begin the related classwork this fall.
“I’m learning so much,” says Ream, who would eventually like to work his way to master electrician. “It’s been so much easier to advance here compared to when I had a desk job. I get raises every six months to a year, and I’m gaining skills that I’ll be able to take with me wherever I go.”
According to Chad Miller, principal at Miller Industries, the apprenticeship program is just one example of how the company helps employees attain new skills. The company also covers training in various subjects including CNC programming, where employees create instructions that allow a computer to control machine tools.
“If we can promote from within, we choose to do that,” Miller says. “But just like anything else, you’ve got to pay your dues first. This means showing up to work on time, having a sense of urgency and doing the work that’s put in front of you.
“If you can do that, you’ll be around here for a long time.”
A good way to get your foot in the door at Miller Industries is to connect with the company’s HR department. For those without a manufacturing background, Miller recommends the assembler positions. “That’s something we teach here. You just need to be able to read blueprints.”
Regardless of where you start, it’s important to find a company that’s fits with your short-term and long-term goals.
West’s advice? Find a company that values its employees.
“Ask about what types of training they offer,” West says. “If you want to grow in your career, find an employer that will support that movement.”